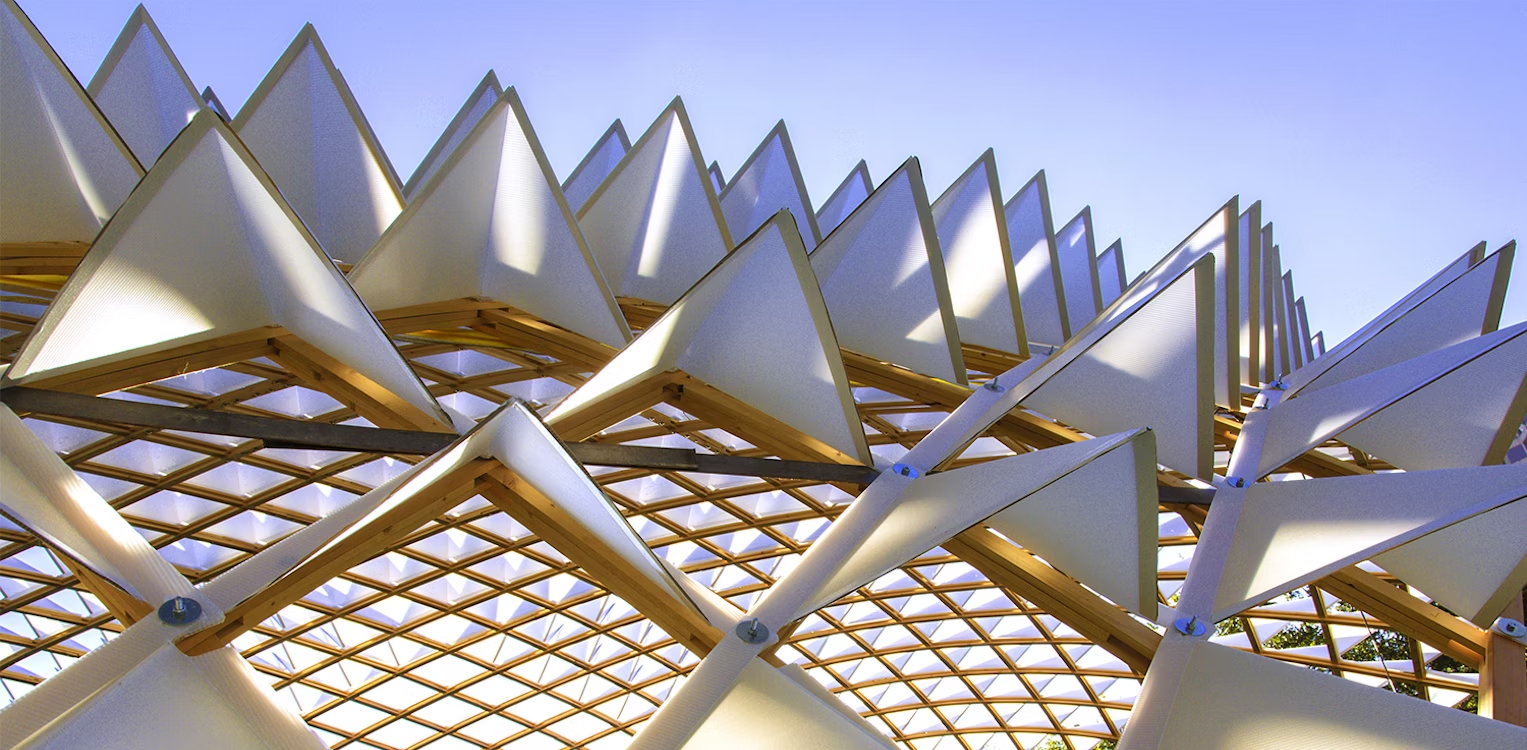
Our Work: Engineered for Design Excellence
As engineers with a passion for architecture, we are driven to empower our clients' vision by providing innovative, design appropriate, and fiscally responsible structural solutions.
Show me solutions engineered for
All Project Types